Concerning LOAK-PROTOTYPE, which features a titanium 3D-printed housing, it hasn’t been on the market for a long time, but as I progressed with its production, a significant issue emerged. I am currently considering whether to continue producing this model or to stop accepting orders for it at a suitable point in our housing inventory, although this decision won’t be immediate. Let me explain the background of this decision.
Instability in Titanium Output through 3D Printing
The issue lies in the lack of stability in the accuracy of titanium housings produced through 3D printing. In comparison to CNC machining, 3D printing introduces subtle size discrepancies, and the outputted housings often exhibit imperfections such as blemishes and irregularities, resulting in only about 50% of the produced housings being usable. The remaining 50% fails to meet the required standards, showing deviations like loss of circularity, blemishes, and irregular layering patterns.
Addressing this requires adjustments in the design phase, such as increasing the thickness of the housing or minimizing abrupt curves. However, after several tests, it became apparent that increasing the housing thickness has limits, especially considering its impact on sound quality. Even with streamlined designs, issues like irregular layering patterns persist, and attempting to polish these patterns introduces size discrepancies.
As a result, I am currently only using the housings that have been successfully printed, leading to a significantly low yield.
Cost-related Challenges
Originally, I anticipated a 20-30% loss during the testing phase for titanium housings produced through 3D printing, and I priced the product accordingly. However, the actual losses in mass production exceeded the initial estimates. The current average rejection rate is around 50%, creating a considerable strain on profits and negatively affecting overall business operations.
Philosophy of Craftsmanship
From the perspective of someone involved in the craftsmanship of creating earphones, producing a product where half of it is unusable is not ideal, even if the other half is profitable. Especially when dealing with the precious material that is titanium, it raises questions about the sustainability of manufacturing when 50% of it goes to waste. In my view, transitioning to a method that eliminates unnecessary waste and achieves a 100% utilization rate is a more sensible approach.
Interruption of LOAK-PROTOTYPE Orders (Planned)
Due to the reasons mentioned earlier, I am considering stopping orders for LOAK-PROTOTYPE in the near future. The decision not to start lending trial units of these models in Japan was also based on this situation. Even if they sell well now, it would actually be inconvenient for me, so I refrained from lending trial units.
Since I still have housing inventory (though not extensive), I will use them efficiently. Therefore, LOAK-PROTOTYPE can still be produced for the time being. If the inventory runs out and there is a strong desire to make more, it might be possible, but the price would likely increase significantly.
LOAK2Titanium Model as an Alternative
With the discontinuation of the LOAK-PROTOTYPE model, there will be no earphones with titanium bodies. However, I have already begun testing a model that will serve as a replacement.
This new model will feature titanium housings created through CNC machining instead of 3D printing. CNC machining, even with multi-axis processing, is limited in creating complex shapes due to cost considerations. As a result, parts like the MMCX section on the LOAK2 model will likely be made of resin.
The housings are already finished, and although the price is quite high, I am arranging production with a facility capable of CNC machining titanium. However, there is a concern related to sound.
While CNC-machined titanium housings are structurally similar to regular titanium, they differ slightly in properties from 3D-printed titanium housings. 3D-printed titanium, as requested by 634EARS, is harder than regular titanium. Hardness in this context means that it maintains its shape without warping. In other words, 3D-printed titanium is less prone to distortion and quickly rebounds the compression of air around the diaphragm, resulting in a tight and crisp sound. On the other hand, CNC-machined titanium is more prone to distortion and has greater strength (meaning it is more likely to bend or flex), which means it might allow the diaphragm to move more freely, potentially altering the sound output from the driver.
While this is speculative until further testing is done, considering the characteristics of the materials, it can be expected that 3D-printed titanium would offer a tight and sharp sound with clear contours, resolution, and focus. In contrast, CNC-machined titanium might provide a broader, more powerful sound.
In conclusion, the future of LOAK-PROTOTYPE production is not yet confirmed, but based on the current situation, it seems challenging to continue. For those who have already purchased LOAK-PROTOTYPE, the sound may be better than that of the alternative model, but the build quality as a product will differ. I intend to accommodate those who wish to exchange their units.
While this is currently a somewhat vague discussion, it is the plan for LOAK-PROTOTYPE to be discontinued in the near future. I will provide further details as soon as they become available.
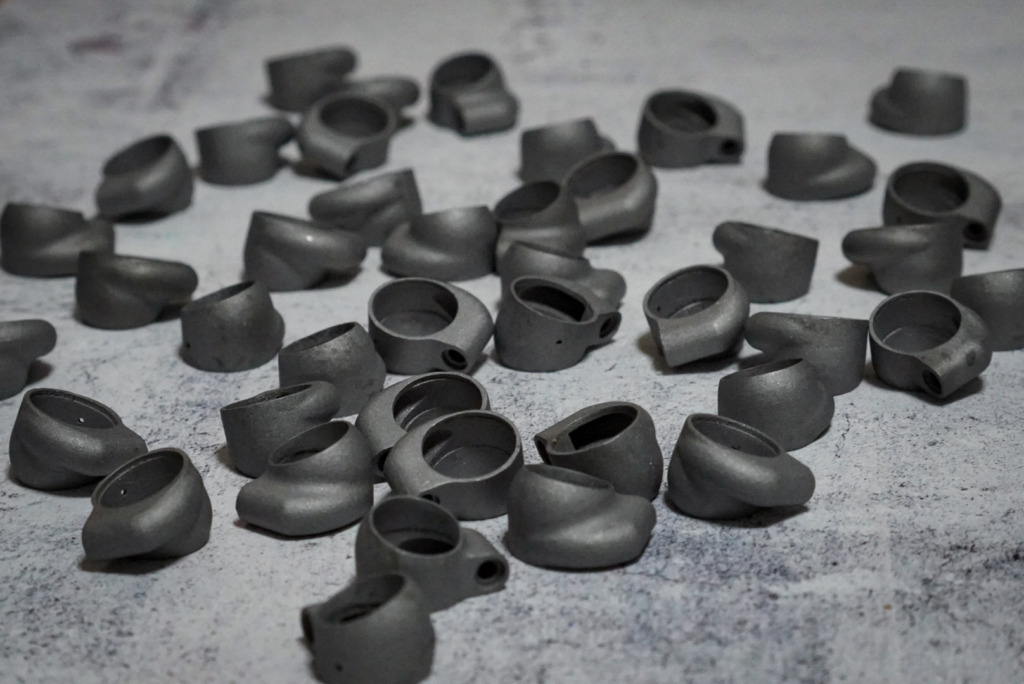